Volvo will ab 2030 nur noch rein elektrische Autos bauen. Der schwedische Hersteller im Besitz der chinesischen Geely Group investiert in den kommenden Jahren insgesamt zehn Milliarden Schwedische Kronen (rund 960 Millionen Euro) in sein Stammwerk Torslanda. Neue Fertigungsprozesse sollen die Produktionsstätte fit machen für die Herstellung der "nächsten Generation von Elektroautos", die 2025 auf einer neuen Architektur debütieren, so Volvo.
Dabei ist Volvo auch die Nachhaltigkeit der Produktion wichtig. In einer 2021 veröffentlichen Life-Cycle-Analyse (LCA) verglich der Hersteller die Treibhausgas-Emissionen von E-Autos über den gesamten Lebenszyklus von Produktion über Gebrauch bis Recycling mit denen von Verbrennern und ermittelte zwar die erheblich günstigere Gesamtbilanz für das Elektroauto, aber auch drastisch höhere Treibhausgas-Emissionen (THG) bei dessen Herstellung – auch der Batterie-Produktion wegen.
500.000 E-Auto-Akkus von Northvolt
Die Akkus kommen bei den Schweden künftig aus einer gemeinsamen Fabrik mit Northvolt, die ab 2025 in Betrieb gehen und 3000 Arbeitsplätze in Göteborg schaffen soll. Das Werk soll in der Endstufe eine Jahresproduktion von 50 GWh haben, was etwa 500.000 E-Autos entspricht. Die Energieversorgung soll aus erneuerbaren Quellen kommen und den Schweden helfen, ihr Ziil der CO2-neutralen Produktion zu erreichen.
Als weiteren großen Treibhausgasemittent bei der Herstellung von E-Autos hat Volvo in seiner Analyse Aluminium identifiziert, das für die Akku-Gehäuse und zur Gewichtsreduktion bei der Karosserie verstärkt zum Einsatz kommt. Hier setzt das Investment in Torslanda an: Neben der Modernisierung der Lackier- und Fertigungshallen soll vor allem das so genannte Mega-Casting-Verfahren für Aluminium-Karosserieteile Energie-, CO2- und Kosteneinsparungen bringen. Mega-Casting ermöglicht Aluminium-Karosseriefertigung aus einem Guss. Das Verfahren hat E-Auto-Pionier Tesla bekannt gemacht.
Alu-Gussteile statt 100-fach geschweißtes Blech
Im Prinzip ersetzt es geschweißte Stahlbleche bei tragenden Karosseriestrukturen durch sehr große Aluteile aus einem Guss. Der Größe der Teile wegen heißt das Verfahren Mega- oder sogar Giga-Casting (Casting engl. für Gießen) und gilt als Voraussetzung für eine weitere E-Auto-Technologie, das sogenannte Cell-to-Chassis-Design. Dabei sollen die Batteriezellen von E-Autos direkt in die Karosse des E-Autos eingebaut werden, was Platz spart und für eine erheblich gesteigerte Energiedichte des Gesamtsystems Akku sorgen soll. Tesla hat es auf dem Battery Day 2020 vorgestellt.
Im ersten Schritt ist bei Volvo aber noch kein Einbau der Batteriezellen direkt in Karosseriestrukturen geplant. Zunächst stellen die Schweden nur den hinteren Teil der Bodengruppe verschiedener E-Autos im Mega-Casting-Verfahren aus Aluminium her. Die Auswirkungen sind aber laut Mikael Fermér, dem verantwortlichen Volvo-Entwickler, trotzdem beachtlich: Die Gewichtsersparnis betrage mindestens 15 Prozent.
Weniger Ausschuss dank Alu
Außerdem sinke die Komplexität erheblich, weil ein neues Alu-Gußteil quasi 100 Stahlbleche ersetzt, die zuvor verschweißt werden müssen. Das wiederum mache zudem den Einsatz von Alu um 35 Prozent CO2-ärmer – bei Aluminiumguss gibt es laut Fermér praktisch kein überschüssiges Material, während beim Stanzen oder Schneiden der Stahlbelche ca. 50 Prozent Verschnitt anfalle; man ersetze also die Menge verwendeten Stahls durch halb so viel Aluminium, das aus Recycling kommen könne. Volvo strebe eine Quote von 50 Prozent an, wobei eine höhere nur von der Verfügbarkeit abhänge. Um die THG-Emissionen weiter zu senken, kaufen die Schweden Alu bei Herstellern, die weniger als 4 kg CO2 bei der Herstellung eines Kilogramms Aluminium emittieren.
Neben Gewichts-, Kosten- und CO2-Vorteilen geben die Mega-Casting-Teile laut Hersteller außerdem den Designern neue Freiheiten – sie könnten den verfügbaren Platz im Passagier- und Gepäckraum besser nutzen, so Volvo.
Auf die Frage, ob Volvo die größeren Freiheitsgrade künftig auch für die Integration der Batteriezellen in die Karosse nutzen wolle, sagt Fermér, das sei nicht geplant, zumindest noch nicht. Gut möglich also, dass sich Volvo sich auch noch auf diesen Weg macht.
Einfachere Modifikationen, schneller neue Modelle
Aber der Entwickler weist noch auf einen anderen großen Vorteil Mega-Casting-Bodengruppe hinten hin: Bei E-Autos trage diese viel Technik, die Komplexität und Segment des Modells bestimme. Darum sei es sehr vorteilhaft, wenn der hintere Boden als ein Stück in die Produktion einfließe. So seien mehr recht verschiedene Modelle auf einer Linie herstellbar, weil es genüge, ein anderes Bodenteil zuzuführen.
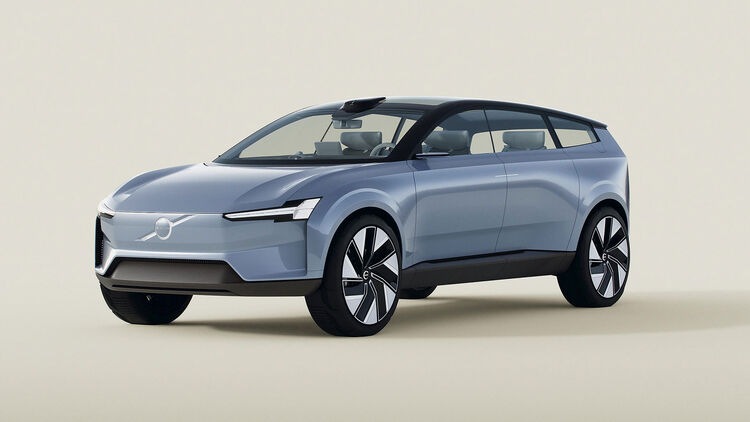
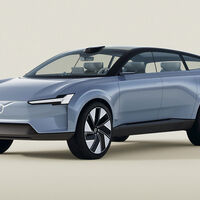
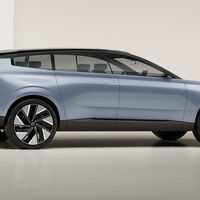
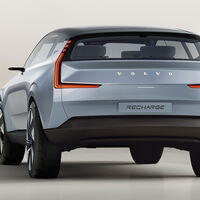
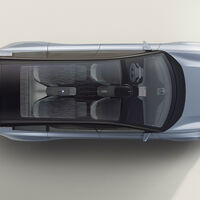
Und vielleicht noch wichtiger: Weiter- oder Neuentwicklungen sind ebenfalls deutlich einfacher und schneller in die Produktion zu integrieren. "Lange Entwicklungszeiten machen ja neue Autos oft schon wieder alt, wenn sie gerade in die Serienproduktion gegangen sind. Wollte man bislang beispielsweise einen neuen Motor auf der Hinterachse oder eine Allradlenkung einführen, ging das selten ohne Produktionsstopp wegen des Umbaus der Linie. Ein neues Mega-Casting-Teil mit sehr ähnlichen Abmessungen ans Band zu bringen ist hingegen viel einfacher". Und die Entwicklung des neuen Teils könne parallel passieren, im Zweifel brauche man einen neue Form oder ein neues Werkzeug, beides hinge aber eben nicht im Fließband.
Fazit
Volvo stellt sich konsequent auf E-Autos um. Das passt zum höheren Ziel der CO-Neutralität. Damit die Schweden die auch mit der energieintensiveren Produktion von E-Autos erreichen, gestalten sie ihre Herstellungsprozesse genauso konsequent um. Technologisch bleibt der Erst-Einsatz von Mega-Casting bei Volvo noch hinter den weit über den Ideenstatus hinaus gediehenen Ansätzen von Tesla zurück – von Cell-to-Chassis scheint Volvo noch weit entfernt.
Auf den zweiten Blick sind sowohl die Einsparungen von Ressourcen und die flexiblere Produktion aber wichtige Zukunftsbausteine, die Volvo für eine neue E-Auto-Architektur ab 2025 gut brauchen kann.