In einer Life-Cycle-Analyse hat Volvo ermittelt, dass die Produktion des E-Autos XC40 Recharge 70 Prozent mehr Treibhausgase (THG) emittiert als die des Verbrenner-Parallelmodells XC40. Dieser Umstand hat in der Vergangenheit Zweifel an der Nachhaltigkeit des Elektroautos geweckt. Tatsächlich zeigt die LCA-Studie von Volvo aber auch, dass das E-Auto über die ganze Lebensdauer auch dann CO2-ärmer unterwegs ist, wenn es mit dem globalen Strommix fährt, der nur zu 25 Prozent aus regenerativen Quellen entsteht.
Das liegt daran, dass die THG-Emissionen in Relation zu denen der Betriebszeit absolut betrachtet erheblich geringer sind. Entsteht der Ladestrom zum Betrieb aus regenerativen Quellen, sinken die entsprechenden CO2-Emissionen dabei nahe Null. Dann verschiebt sich der Fokus bei der Suche nach Einsparungsmöglichkeiten für THG-Emissionen des Elektroautos von der Nutzung auf die Herstellung. Darum ist es wichtig zu wissen, woher der 70-prozentige Aufschlag kommt.
7 Tonnen CO2 für die Batterieherstellung
Laut Volvo stammen allein 30 Prozent daraus, dass bei Elektroautos mehr Aluminium (vor allem für das Akkugehäuse) und andere CO2-intensive Materialien zum Einsatz kommen, 40 Prozent rühren laut Volvo von der Herstellung der Batteriemodule selbst. In absoluten Zahlen sind das im Falles des Elektro-Volvos mit seiner 78 kWh großen Batterie 7 Tonnen, den Mehraufwand für das restliche Fahrzeug beziffern die Schweden mit 4 Tonnen Treibhausgasen.
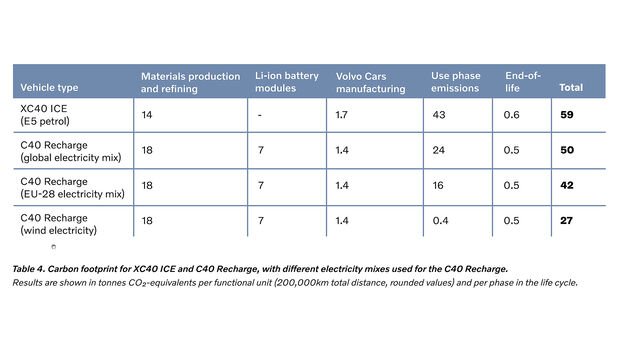
Warum ist die Herstellung von Batteriezellen und Modulen so CO2-intensiv? Um das zu klären lohnt es sich, Funktionsweise, Aufbau und Herstellung der aktuell gebräuchlichen Lithium-Nickel-Mangan-Kobalt-Batterien (Li-NMC) anzusehen. In einer solchen Zelle wandern Lithium-Ionen zwischen einer Kathode aus Nickel (inzwischen gut 80 Prozent), Mangan und Kobalt(oxid) (inzwischen oft unter 10 Prozent) und der Anode aus typischerweise Graphit hin und her. Legt man an die Pole einen (Lade)strom an, lagern sich die positiv geladenen Lithium-Ionen im Graphit an der Anode an (Interkallation). Beim Entladen wandern sie durch den Elektrolyt und einen Separator zwischen den Elektroden zur Kathode zurück. Die Anode ist dadurch negativ geladen, weshalb an ihrem äußeren Pol Elektronen abfließen – der zum Antrieb nutzbare Strom.
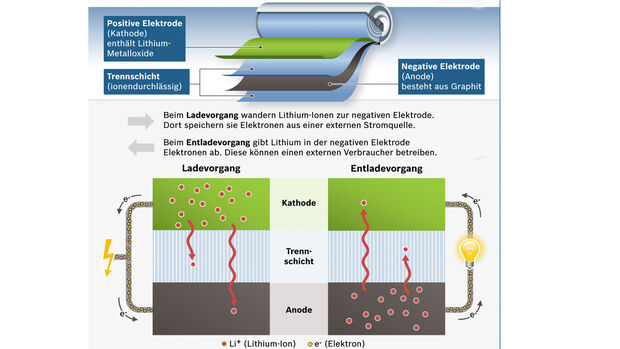
Akkus aus dünnsten Schichten
Modelle zur Veranschaulichung der Funktionsweise gaukeln nennenswerte Abstände zwischen den Komponenten vor – in der Realität bestehen Elektroden und Separator aus dünnsten Schichten, die mehr oder minder eng aufeinander liegen, wie dieses Bild aus einer Tesla-Rundzelle zeigt; aber auch in Pouch- oder prismatischen Zellen ist der Aufbau sandwichartig mit sehr dünnen Schichten.
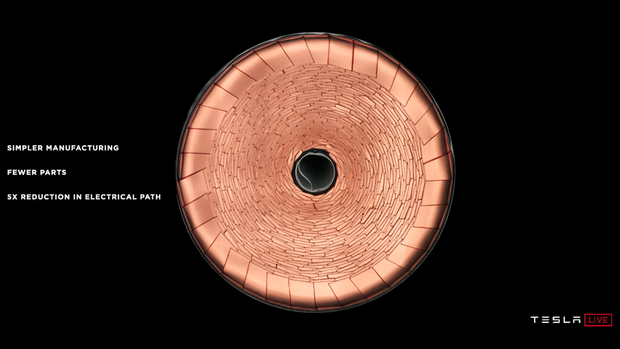
Die Elektrodenmaterialien entstehen in mehrstufigen chemischen Prozessen. Beim Kalzinieren des Li-NMC fährt das Material gegen den Wärmestrom durch einen Ofen mit Temperaturen von 800 bis 1.000 Grad. Der Prozess muss sehr exakt ablaufen, weil er die genaue Zusammensetzung und die Reinheit des Kathodenmaterials bestimmt. Das Graphitisieren von Soft-Carbon für die Anode erfordert noch höhere Temperaturen: Bei 1800 bis 3000 Grad durch Anlegen von Spannungen von 40.000 bis 50.000 fließen Ströme von 200 Ampere und verbrennen auch kleinste Verunreinigungen.
Akkuherstellung "verheizt" Energie
Zu Beginn liegen Anoden- und Kathoden-Materialein zunächst in Pulverform vor. Die Mischung mit Lösungsmitteln, oft organische Materialien (inzwischen versucht man dafür Wasser zu verwenden), lässt den so genannten Slurry (Pampe, Brei) entstehen. Über 90 Prozent des Festmaterials in dieser möglichst homogenen Suspension sind Aktivmaterial. Dazu kommen dann noch Bindemittel (Polymere) und Leitfähigkeitsadditive. Die Suspension muss in einer exakt definierten Höhe bzw. Gewicht pro Fläche auf eine sehr dünne Kupfer- oder Alufolie – in der Dicke durchaus vergleichbar mit denen, die wir aus dem Lebensmittelbereich kennen. Das geschieht mittels verschiedener Techniken: Sprühen, Rollern, Drucken – alles ist möglich. Es sollte nur auf möglichst breiten, langen Bahnen (für eine hohe Produktionsgeschwindigkeit) so gleichmäßig wie möglich passieren, um den Ausschuss zu minimieren. Der erzeugt am Ende Zellen, die nicht funktionieren, in denen aber schon ordentlich Energie zur Herstellung steckt. Richtig Energie und damit auch Treibhausgasemissionen stecken aber vor allem im an sich simplen Entfernen des Lösungsmittels – es trocknet einfach aus. Aber dazu fährt die beschichtete Folie durch einen riesigen, langen Durchlaufofen.
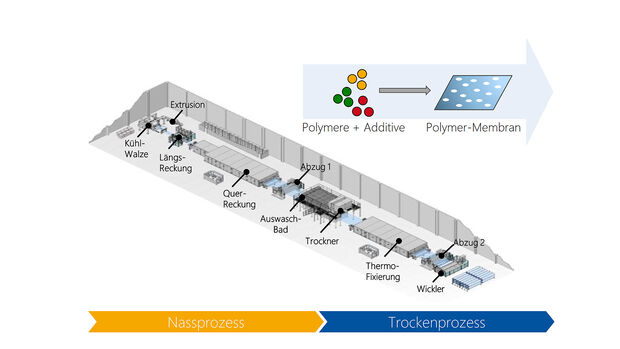
Die ähnlich dünne Separatorfolie (aus einem Polymer) verbindet sich mit den Additiven unter Druck und bei hohen Temperaturen (200 bis 240 Grad), aufgebrachtes Lösungsmittel muss auch hier wieder verdunsten, die meiste Zeit läuft die Folie über Walzen, wird in zwei Richtungen (biaxial) gedehnt (verstreckt) und läuft vor allem ebenfalls durch einen Trocknungsofen. Das PEM (Production Engineering of E-Mobility Components) der RWTH Aachen gibt an, dass ein solcher Ofen bis zu 110 Meter lang sein kann. Bei einer Folienbreite von 5,5 Metern ist die Ofenfläche also mindestens 605 Quadratmeter groß. Während der abschließenden Thermofixierung beträgt die Temperatur 120 bis 140 Grad – eine sehr heiße Riesen-Sauna mit entsprechendem Energiebedarf.
Das Ganze gilt übrigens auch für die Akkus von Smartphones oder Laptops und nicht nur für die von E-Autos – aber die sind halt besonders groß und der Bedarf steigt stark an.
Sparsamere Elektrodenproduktion?
Um den Energieaufwand zu reduzieren arbeitet Tesla beispielsweise an einem Verfahren mit einer Trockenbeschichtung der Batteriefolien – das Austrocknen des Lösemittels entfiele. Das haben die Amerikaner allerdings bereits im September 2020 angekündigt, der Entwicklungsstand ist aktuell nicht bekannt. Das Karlsruhe-Institut für Technologie (KIT) arbeitet an einer Beschleunigung des Verfahrens, das die Energiekosten immerhin um 20 Prozent reduzieren soll. Die vergleichsweise junge Herstellungstechnik für Lithium-Ionen-Batterien scheint also durchaus noch Potenzial zu bieten.
Eine andere Zellchemie wie etwa Lithium-Eisenphosphat ändert am Energiebedarf hingegen übrigens wenig – vom Energieaufwand für die Herstellung der Materialien mal abgesehen.
Energie für Akkuproduktion muss möglichst grün sein
Entscheidend ist also, dass die Energie für den Strom zur Batterieherstellung aus regenerativen Quellen kommt. Das zeigt eine Studie der Uni Trier eindrucksvoll. Electrive zitiert Eckard Helmes, einen der Autoren der Studie: "Im schlechtesten Fall kann die Batterie 36 Prozent der gesamten Lebenszeit-CO2-Emissionen eines Elektroautos ausmachen", sagt Helmers. "Ich denke, am Vorabend von Milliardeninvestitionen in neue Batterieproduktion sollte dieser Aspekt betont werden." Der schlechteste Fall ist in der Studie "Batteriezellen aus China". Denn dort emittiert die Stromerzeugung 1.180 Gramm CO2-Äquivalent pro Kilowattstunde, beim europäischen Strommix sind es hingegen lediglich 531 Gramm, in Deutschland geht das Umweltbundesamt für 2020 gar von 366 g/kWh aus. In unserer Bildergalerie zeigen wir die Batteriefabriken in Europa.
Die Autohersteller haben den Zusammenhang erkannt und bemühen sich darum, für ihre neuen Batteriefabriken auch eine Grünstromversorgung einzuplanen oder einplanen zu lassen. VW und BMW etwa kooperieren mit Northvolt. Emma Nehrenheim, Leiterin der Umweltabteilung des schwedischen Unternehmens, sagt in einem Interview: "Um die grünste Batterie der Welt zu bauen, ist eine saubere Energiebasis für die Herstellung absolut notwendig. (..). Wir haben dies sichergestellt, indem wir unser Werk Northvolt Ett mit 100 Prozent emissionsfreiem Strom versorgen, der größtenteils aus Wasserkraft in Nordschweden stammt. Allein dadurch wird sich der Kohlenstoff-Fußabdruck der Zellen um mehr als 50 Prozent verringern – im Vergleich zu einer Anlage, die beispielsweise über das südkoreanische Stromnetz versorgt wird."
Wasserkraft mag es nicht überall massenhaft geben. Aber die Trierer Studie weist der Stromerzeugung durch Solaranlagen auch nur 92 Gramm und Windkraft sogar lediglich 15,8 Gramm Treibhausgasemissionen pro kWh zu.
Fazit
Der große CO2-Rucksack des Elektroautos stammt vor allem von der energieintensiven Herstellung der Akkus, bei denen wiederum die Fertigung der Elektroden und Separatoren die meisten Energie braucht. Ob und wie schnell deren Produktion dank neuen Methoden künftig mit weniger Strom auskommen kann, ist unklar. Nicht nur bis dahin ist eine grüne Stromerzeugung für die Akku-Produktion essenziell. Sie kann den CO2-Abdruck der Batterie um ein 30 bis mehr als 50 Prozent verkleinern.
Den noch größeren Hebel bietet aktuell die Dekarbonisierung des Fahrstroms. Die Volvo-Life-Cycle-Analyse gibt für die Batterieproduktion THG-Emissionen von 7 Tonnen an. Die Annahme von 1000 Prozent regenerativem Strom zum Laden des XC40 Recharge sparte gegenüber dem Weltenergiemix mit 25 Prozent Grünstrom-Anteil über die gesamte Lebensdauer 23,6 Tonnen an CO2-äquivalenten Emissionen.