(Lacht). Ich bin seit über 20 Jahren bei BMW und dieses Jahrhundert-Projekt ist sicher die Kür meiner Laufbahn. Als ich von unserem Vorstandsvorsitzenden Oliver Zipse gefragt worden bin, ob ich diese Aufgabe übernehmen möchte, habe ich sofort zugesagt. Wir führen mit der Neuen Klasse BMW aus dem Kern der Marke heraus in die Zukunft – mit einer völlig neuen Modellgeneration und neuesten Technologie-Clustern. Diese Chance, das zu gestalten, ist natürlich einzigartig. Als Chefingenieur habe ich unsere heutige Cluster-Architektur um die rein elektrischen Modelle wie i4, i7 und i5 erweitert. Die Neue Klasse ist nun eine ganz besondere Aufgabe, weil wir sie auf dem weißen Blatt Papier anfangen durften.
Ich bin seit 2020, also seit der ersten Stunde in der Verantwortung. Das Projekt selbst trägt eine kleine Führungs-Mannschaft. Uns steht ein großes, übergreifendes Projekt-Team aus allen Ressorts und allen Fachabteilungen des Unternehmens zur Verfügung. Entscheidend ist dabei, dass die Abteilungen, die es später umsetzen müssen, von Anfang an dabei sind. Wenn einer ein Konzept vorgibt, und der Rest der Mannschaft kommt erst später dazu, entstehen Brüche. Bei uns wurden deswegen ganz früh die relevanten Disziplinen integriert.
Wir sind jetzt in einer Phase der Generationssprünge. Die Entwicklung von Batteriezellen beispielsweise ist so dynamisch, dass exakte zeitliche Vorhersagen für den Sprung von unserer flexiblen in eine BEV-Only-Architektur zu schwer zu treffen sind. Aber ich bin überzeugt, dass wir mit unserem Produktionsstart für den Erstanläufer der Neuen Klasse in 2025 sehr, sehr gut liegen.
Das war im Frühjahr 2022 etwa. Die ersten zwei Jahre haben wir das Projekt strategisch ausgerichtet und die Grundsatzentscheidungen getroffen. In dieser Phase war der Direct-Report an den Vorstandsvorsitzenden genau richtig. Trotzdem war das Projekt-Team schon damals crossfunktional aufgestellt. Inzwischen ist es riesig: Heute arbeiten rund 7.000 Mitarbeiter an der Neuen Klasse.
In Debrecen/Ungarn wird ein neues Werk gebaut, in dem das erste Modell der Neuen Klasse, das SAV, anläuft. Die Arbeiten laufen auf Hochtouren, parallel fünf Hochvoltbatterie-Montagen weltweit. Nachdem nach zwei Jahren die Weichen gestellt waren, wurde es Zeit in die Umsetzungsorganisation zu wechseln, die den Prototypen-Bau und die Industrialisierung sicherstellen muss.
Am Ende sind das auch Zielkonflikte – und damit müssen Entwickler umgehen. Wir überlegen, wie man die auflösen kann, wie schon bei Efficient Dynamics. Man versucht, mehrere Funktionen gleichzeitig zu erfüllen. Nachhaltigkeit geht einher mit Effizienz. Die steigert die Mobilität, weil sie Reichweite generiert. So gelangt man vom Großen zum Konkreten. Welche Ziele wähle ich, wie integriere ich sie, welche Effizienz-Ziele nehmen wir uns dementsprechend vor? So entwickelt sich das Anforderungsziel jeder Komponente. Wie hoch kann der CO₂-Einspar-Beitrag dieser Komponente sein, um das gesamthafte CO₂-Ziel zu erreichen? Dafür wählen wir eine komplett andere Arbeitsweise: Wir entwickeln uns von Kooperation zu Kollaboration. Wir bringen Experten zum richtigen Zeitpunkt crossfunktional zusammen, um schneller, agiler zu sein.
Es gibt einen großen Unterschied: Project i war damals so ein Pionier, dass man versucht hat, es vom klassischen Serien-Geschäft zu entkoppeln, damit die Projektgruppe andere Freiheitsgrade nutzen konnte. Unser Projekt hat das umgekehrte Ziel: Die Marke im Kern zu transformieren. Es war von Anfang an vollkommen klar: Das Projekt startet im Kern von BMW, es wird nicht eine separierte Truppe sein, sondern die verantwortlichen Kompetenzzentren sind Teil der Projekt-Mannschaft. Das Projekt "Neue Klasse BMW" sollte alle anderen integrieren, damit das gesamte Unternehmen von den Technologiesprüngen und Entwicklungen der Neuen Klasse profitieren kann. Die Neue Klasse wird das gesamte zukünftige BMW-Portfolio auf ein neues Level heben.
(Lacht) Weil’s eh klar ist.
Die Neue Klasse macht einen riesigen Sprung. Zentral sind die Fortschritte bei den Batteriezellen. Wir werden allein im Antriebsstrang im Vergleich zu heute zirka 40 Prozent Herstellungskosten reduzieren. Das wird noch nicht ganz reichen, um auf Augenhöhe mit dem Verbrenner zu sein. Andererseits ist heute ein Diesel auch teurer als ein Ottomotor – dafür verbraucht er weniger, der Kunde bekommt also quasi Kosten zurück. Die nächste BMW Modellgeneration wird in Sachen Effizienz mit bis zu 25 Prozent Steigerung jedenfalls noch einmal einen deutlichen Hub machen.
Wir haben einen ambitionierten Plan, aber absolute Volumen nennen wir nicht. Im Jahr 2025 starten wir die Produktion unseres ersten Modells der Neuen Klasse in unserem neuen Werk in Debrecen. Wir planen einen schnellen Rollout – wir bringen sechs Modelle innerhalb von 24 Monaten. Bis 2030 wollen wir einen Absatz von mindestens 50 Prozent batterieelektrischer Fahrzeuge erreichen.
Nach meiner Einschätzung sind alle drei gleichwertig, aber von unterschiedlichem Charakter. Ich denke, mit der Neuen Klasse sind die Pain Points der Elektrifizierung für den Kunden gelöst – die wir über das Auto beeinflussen können.
Dann geht es um Herstellungskosten. So dynamisch wie die Entwicklung aktuell ist, muss man genau aufpassen, dass man immer die modernste Zelltechnologie am Start hat, um die Sprünge mitzunehmen. Die Digitalisierung ist das schnelllebigste: permanente Over-the-Air-Update-Fähigkeit, neue Geschäftsmodelle – das könnte für den Kunden das Wichtigste sein.
Das langfristige ist sicherlich die Kreislauffähigkeit. Wenn ein 2025er-Fahrzeug zurückkommt – vielleicht frühestens 2040 – ist jetzt die Hauptaufgabe zu überlegen: Wie gestalte ich heute, damit dann die Materialien ideal wieder eingesetzt beziehungsweise wiederverwertet werden können. Gleichzeitig gilt heute schon, wo kann ich jetzt schon sekundäre Materialien einsetzen? Was ist heute an Sekundärmaterial verfügbar, wie können wir die künftige Verfügbarkeit heute anstoßen und vordenken.
Es ist bahnbrechend, das Auto als Teil eines geschlossenen Lebenszyklus zu denken. Es beginnt mit der Frage, wie viel sekundäre Rohstoffe kann ich heute schon beim Produzieren einsetzen? Es geht weiter mit dem CO₂-Footprint und der Vermeidung von Abfällen bei der Herstellung, der Effizienz während der Fahrt sowie dem Rückführen und Wiedereinsetzen von Materialien.
Hilfreich. Die Materialien in der Zelle beispielsweise sind teuer und schwer verfügbar. Technisch möglich ist heute über 90 Prozent der Materialien einer Hochvoltbatterie am Ende des Lebenszyklus' wieder so aufzubereiten, dass wir sie dann wieder für neue Zellen nutzen können – ohne Einfluss auf die Performance des Speichers. Allerdings gibt es heute gar nicht so viele ältere batterieelektrische Fahrzeuge, aus denen wir schon genug neue Zellen für den Hochlauf gewinnen könnten. Insgesamt wird das ein Prozess, bei dem man immer wieder Lieferketten und das Schließen der Kreisläufe bei den Lieferanten anstoßen muss.
Wir sind überzeugt: Man muss die Zellen im Detail verstanden haben, weil das letztlich entscheiden wird, welche Performance der Kunden bekommt, aber auch welche Kosten entstehen. Vieles davon steckt auch im Fertigungsprozess. Aber die Zellentwicklung ist schnelllebig – von neuen sogenannten "Superbatterien" lesen wir nahezu täglich. Aber ob heute getätigte Investitionen in eine Großserienproduktion in drei Jahren noch gerechtfertigt erscheinen, halte ich für extrem schwer zu beurteilen. Deswegen bin ich überzeugt, dass es richtig ist, mit den wichtigsten Partnern eigenes Knowhow aufzubauen und offen zu sein.
Wir fahren hier einen sehr klaren Ansatz: in unserem Kompetenzzentrum Batteriezelle in der Nähe des FIZ stellen wir sicher, dass wir Chemie und Format der Zelle zu 100 Prozent verstehen. In unserem Kompetenzzentrum Zellfertigung – in Parsdorf – vor den Toren Münchens, ist unsere Musterfertigung. Mit der Bündelung dieser beiden Kompetenzen – Entwicklung und Fertigung – stellen wir sicher, dass unsere Partner, die für uns beste Zellen produzieren und liefern können. Wir sind sicher, dass diese Strategie der für uns richtige Weg ist.
Ja. Denn eigentlich haben wir ein Energie-Modul geschaffen. Das ist wie ein großer, für den Speicher reservierter Energiebauraum, den wir mit Zellen füllen, ohne dass wir das Auto oder seine Architektur variieren müssen. Das ist ein nächster Schritt nach unseren aktuellen Gen-5-Batterien und macht uns flexibel für die Zukunft. Wenn es eine effizientere Chemie gibt, kann sie rein, wenn All-Solid-State kommt, kann das genauso ins Fahrzeug.
Wir arbeiten mit Li-NMC, über die Spezifika der Chemie kann ich nichts sagen. Was aber schon wichtig ist: Die großen Rundzellen bringen eine signifikante Steigerung der Energiedichte von 20 Prozent. Wir haben aber noch zwei weitere Faktoren, die den großen Sprung bei der Reichweite ermöglichen: Das eine ist Effizienz. Es macht keinen Sinn, immer größere Speicher zu integrieren. Die Frage ist vielmehr: Wie weit kann ein Fahrzeug mit existierenden Speichern fahren? Da werden wir einen großen Sprung machen. Und der dritte Faktor ist die bereits erwähnte Flexibilität des Speichers.
Der wesentliche Sprung kommt von der 800-Volt-Spannungslage. Aber Detailoptimierung ist ebenfalls sehr wichtig. Ohne eine gleichmäßige Kühlung aller Zellen lässt sich die hohe Ladeleistung nicht umsetzen.
Wir haben aktuell drei Partner nominiert: CATL sowie Eve für Europa und Asien und Envision (AESC) für Nordamerika. Die fahren ihre Produktion sukzessive mit unseren Fertigungsstandorten hoch. Die Performance der Zelle fürs Fahrzeug wird immer die gleiche sein, egal, von welchem Partner sie kommt.
Das Thema Haltbarkeit von Zelle und Speicher ist natürlich eines der wichtigsten und darum ist gesetzlich beispielsweise streng geregelt, wie viel Reichweite nach wie vielen Jahren möglich sein muss. Wir werden alle Langlebigkeitsanforderungen erfüllen. Wie gut der Akku hält, hängt aber am Ende auch stark von der Nutzung ab. Ob DC- oder AC-Laden ist auf Dauer vielleicht sogar weniger entscheidend, als etwa, ob immer zu 100 Prozent vollgeladen wird. Wir sagen ja immer: Von 10 bis 80 Prozent ist der Bereich, in dem sich der Speicher sehr wohlfühlt.
Wir werden die Akkus der Generation 6, also für die neue Klasse, so auslegen, dass wir von Anfang an bidirektional laden können. Aber es gibt ja unterschiedliche Use Cases. Wenn der Speicher des Fahrzeugs beispielsweise das Haus versorgen soll, muss man darauf achten, wie viel man freigibt, ohne in die Grenzbereiche zu kommen. Bei der Nutzung der Batterie zum Betreiben externer Verbraucher unterwegs etwa, wird das nicht der Fall sein. Zudem gibt es unterschiedliche Konzepte, AC und DC. Wir sind am beidem dran.
Das Wichtigste ist, dass wir für die Herstellung so viel sekundäre Rohstoffe wie möglich und Mono-Materialien verwenden. Denn am Ende sind es oft die Material-Mixe, die es schwierig machen. Das Demontagekonzept muss man dann in die Verwerter-Betriebe tragen, die das Auto und seine Teile am Ende zerlegen. Wir selbst haben beispielsweise darauf geachtet, dass alles, was an der Batterie servicebar sein muss, nicht im Speicher selbst angeordnet ist. Die gesamte Elektronik, die Steuerung ist zugänglich und lässt sich tauschen, ohne den Speicher zu öffnen. Und wir haben die Bauweise von Zelle, Modul, Speicher, Karosserie so geändert, dass deutlich weniger Teile nötig sind.
Der Speicher selbst entsteht unter höchsten Qualitätsanforderungen, damit es genau das nicht braucht.
Ja, es wird immer so sein, dass man den Speicher tauschen kann – mit entsprechendem Aufwand. Der entsteht heute auch beim Tausch des kompletten Antriebsstrangs eines Verbrenners. Beim E-Auto ist das deutlich aufwendiger. Deswegen ist unsere oberste Priorität: null Fehler.
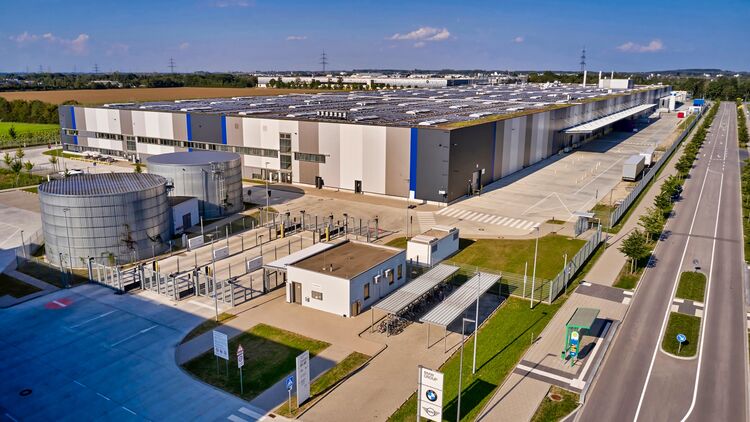
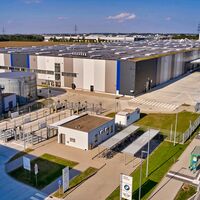
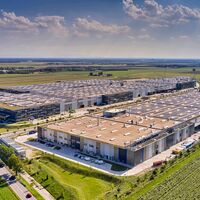
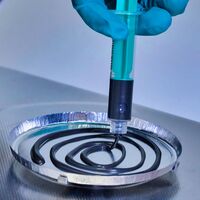
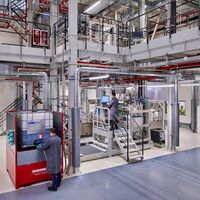
Wir haben auch diesbezüglich viele Erfahrungen gemacht: Der Speicher stellt selbst am Schluss noch einen so großen Wert dar, dass er für andere Zwecke zum Einsatz kommt.
Wir haben heute beides vorgesehen. Der Speicher ist ausbaubar. Wenn er noch gut ist, kann er beispielsweise als Stationärspeicher dienen. Oder er wird dem Recycling zugeführt. Wir haben bereits nachgewiesen, dass wir dabei über 90 Prozent der Rohmaterialien wiederverwenden können, und zwar zur Herstellung neuer Zellen.
Wenn Sie den BMW i Vision Dee von der CES mit dem BMW Vision Neue Klasse vergleichen, können Sie die Konstanten ganz gut ableiten. Das Serienauto wird schon eine Ähnlichkeit haben – und beim Bedienkonzept sind wir schon sehr nah an dem, was wir für 2025 vorhaben.
Herr Reichelt, vielen Dank für das Gespräch!
Vita Mike Reichelt
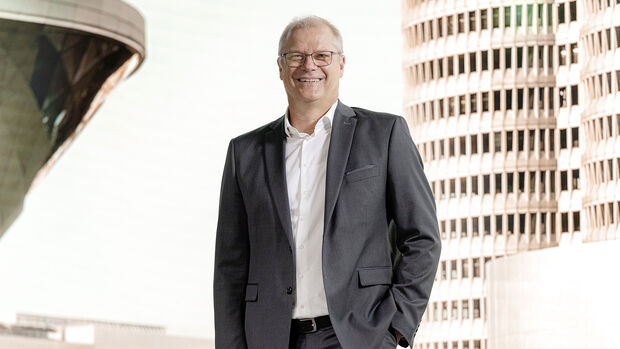
Dr. Mike Reichelt ist (Jahrgang 1970, geboren in Chemnitz) schloss 1995 als Diplom-Ingenieur ein Maschinenbau-Stuium in Chemnitz ab. 1996 fing er bei BMW in München an. Sein Schwerpunkt war zunächst die Karosserieentwicklung. Von 1998 bis 2003 promovierte er nebenberuflich an der Technischen Universität Chemnitz. Thema der Doktorarbeit: "Identifikation schwach gedämpfter Systeme am Beispiel von PKW-Karosserien".
Von 2001 bis 2009 war er bei BMW unter anderem Abteilungsleiter der Abteilung Strukturdynamik und Schwingungen des Fachbereichs Gesamtfahrzeug, von 2009 bis 2015 hatte er eine leitende Funktion für das technische Konzept der Hecklängsantriebsarchitektur (CLAR) und der zugehörigen Gesamtfahrzeuge inne. Von 2015 bis 2019 war er Leiter der Produktlinie Mittelklasse und trug die Gesamtverantwortung für die Derivate 2er bis 6er, X3/X4 (inklusive der batterieelektrischen Varianten).
Seit 2020 ist er Leiter Neue Klasse.