BMW hat nahe München eine neue Pilotanlage zur Batteriezellfertigung eröffnet. Deren erste Aufgabe ist die Produktion neuer Rundzellen, die 2025 erstmals in Fahrzeugen der "Neuen Klasse" zum Einsatz kommen.
Mit dem CMCC (Cell Manufacturing Competence Center, Kompetenzzentrum für Batteriezellfertigung) ergänzt der bayrische Autobauer die Batteriezellforschung, die bereits im Norden von München etabliert wurde. Damit will BMW bei Entwicklung und Produktion von Elektroautos alle Schritte im eigenen Haus behalten. Das CMCC in Vaterstetten-Parsdorf bei München ist dabei das letzte Glied vor der Großserienproduktion von Batteriezellen bei den Zulieferern.
Pilotproduktion für eine Million Batteriezellen
Im CMCC werden also nicht im großen Maßstab Batteriezellen gefertigt. Von der neuen, jetzt sechsten Zellgeneration der Münchner sollen dort rund eine Million Einheiten produziert werden. Das CMCC entwickelt dabei die Produktionsmethoden und Vorgaben, nach denen später Zulieferer in die Massenproduktion einsteigen. Diese neuen BMW-Rundzellen ersetzen die bisher verwendeten quaderförmigen "prismatischen" Zellen. Sie haben einen einheitlichen Durchmesser von 46 Millimetern und zwei verschiedene Höhen von 95 Millimetern und 120 Millimetern. Sie wiegen rund 420 Gramm pro Stück.
Gegenüber der fünften Generation Batteriezellen, die aktuell in BMW Elektroautos wie dem iX verbaut wird, erreichen die neuen Rundzellen eine um über 20 Prozent verbesserte Energiedichte, sind also bei gleicher Speicherkapazität um diesen Faktor leichter als aktuell. Das Ladetempo soll in Verbindung mit der bei der "Neuen Klasse" verwendeten Ladetechnik um rund 30 Prozent steigen. Die technischen Einzelheiten hatte BMW bereits vor einem Jahr kommuniziert, in diesem Beitrag haben wir die Details zusammengefasst.
Im neuen Parsdorfer "Kompetenzzentrum" produziert BMW die Batteriezellen als Kernelement der kommenden Fahr-Akkus aus allen Einzelzutaten, vom Rohmaterial für Anoden und Kathoden bis zur fertigen Rundzelle. Diese Produktion geschieht nach den Vorgaben der hauseigenen Batteriezellforschung und in Abstimmung mit den Antriebsentwicklern. Denn Batterie ist nicht Batterie, betonte Milan Nedeljković, Produktionsvorstand der BMW AG, bei der offiziellen Eröffnung des CMCC im Gespräch. Das Verhalten der Batteriezellen zum Beispiel bei der Energieabgabe sei ganz spezifisch auf die hauseigenen Vorgaben abgestimmt, deshalb könne man auch nicht einfach eine beliebige Batterie eines Zulieferers verbauen.
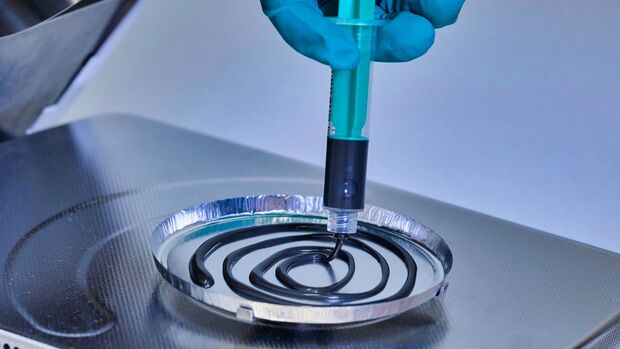
Anfang jeder Batteriezelle: Die "Slurry" genannte Paste, mit der die Anoden- und Kathodenfolien beschichtet werden.
Daher werden bei der Werksbesichtigung einzelne Produktionsschritte nur von außen durchs Fenster gezeigt, die Kameras der Mobiltelefone wurden zuvor abgeklebt, genaue Details werden ebenfalls nicht verraten. Zum Beispiel die genaue Zusammensetzung der "Slurry" genannten Paste. Diese wird aus fünf (Anode) beziehungsweise vier (Kathode) Komponenten zusammengerührt und dann auf die jeweiligen Trägerfolien aufgetragen.
Der genaue Aufbau bleibt geheim
Die extrem dünnen Kathoden- und Anoden-Folien werden nach der Beschichtung in verschiedenen Produktionsschritten getrocknet, gepresst und geschnitten, bis sie schließlich gemeinsam mit der Separatorfolie aufgerollt und in das Metallgehäuse der späteren Batteriezelle gesteckt werden. Die genaue Länge der Folie pro Zelle ("mehrere Meter") bleibt auch geheim, weil sich daraus Rückschlüsse auf die Beschichtung ziehen ließen. In diese Rundzellen wird zum Schluss noch durch ein kleines Loch im Deckel das Elektrolyt gefüllt, bevor sie verschlossen, zum ersten Mal geladen und damit "zum Leben erweckt" werden. Von diesem Zeitpunkt an könnten sie eine "Neue Klasse" mit Energie versorgen.
Die einzelnen Produktionsschritte in der neuen BMW Batteriezell-Fabrik zeigen wir Ihnen in der Bildergalerie.
Fazit
BMW will ganz genau bestimmen, wie die Batterien für die hauseigenen Autos konstruiert und produziert werden. Deshalb entwickelt man das gesamte Paket bis zur fertigen Zelle im eigenen Unternehmen. Nach der Batteriezellforschung ist deshalb die Batteriezellfertigung der letzte Schritt, den das Unternehmen nun mit einer neuen Fabrik nahe München in Betrieb genommen hat. Nach deren exakten Vorgaben wird künftig bei Zulieferern die sechste Generation von BMW-Batteriezellen im großen Maßstab produziert. Die Zukunft ist bereits in Sicht, bald steht bei BMW die Entwicklung von Feststoffbatterien im Fokus.