Mit den so genannten Blade-Batterien (Klingen-Batterie) mischt BYD gerade den E-Auto-Markt auf. Ihren Namen tragen die Akkus wegen der Bauweise: In ein 96 Zentimeter breites, 13,5 Zentimeter hohes und nur 1,6 Zentimeter dünnes Alugehäuse packt BYD 155 Folienschichten, davon 38 Kathoden-Folien, 39 mit aufgebrachtem Anodenmaterial (vor allem Graphit) und 78 Isolationsschichten. Von den derart zusammengesetzten "Blades" sitzen im Akkupack des ersten Modells BYD Han 175 Stück senkrecht, so dass die Batterie von oben offen ein bisschen wie ein Nassrasierer aussieht – daher der Name.
Gute Energiedichte mit günstiger Chemie
Die spezielle Bauweise war der Kniff, mit dem BYD eine ausreichende Energiedichte für Autos erreichen konnte, obwohl die Zellchemie an sich der von herkömmlichen Lithium-Nickel-Mangan-Kobalt-Akkus (Li-NMC) deutlich unterlegen ist. Denn BYD verwendet für Traktionsbatterien Lithium-Eisen-Phosphat (LFP). Dieses Material neigt weniger zum thermischen Durchgehen, sprich die Batterien haben ein geringeres Brandrisiko, was sie besonders als Heimspeicher qualifiziert, wo es auf die Energiedichte nicht so ankommt. BYD weist darauf hin, dass die Blade-Batterie die Einzige ist, die den Nageltest besteht. Dabei wird die Zelle von einem Nagel durchbohrt (siehe Video). Während die prismatische Li-NMC-Zelle dabei geradezu explodiert, verläuft der Test bei der Blade-Batterie unspektakulär: es passiert – nichts.
Das ist allemal beeindruckend, auch wenn ein Experte schon 2018 darauf hinwies, dass der Test nicht aussagekräftig genug sei, um zumindest innerhalb von streng vorausgewählten Zellen Unterschiede zu zeigen. Aber der Nagel erzeugt einen internen Kurzschluss mit einem anfangs sehr hohen Strom. Wo der Nagel eintritt, entsteht ein Hotspot, der entflammbare Elektrolyt gast durch die Einstichstelle aus. Manche Zellen kühlen anschließend langsam wieder ab, andere brennen bis zum sogenannten Thermal Runaway, der nur schwer zu löschen ist und der sich auch noch mit großer Verzögerung ereignen kann. BYD sagt, grundsätzlich könnten auch Blade-Batterien in Brand geraten, aber mit geringerer Wahrscheinlichkeit – und vor allem nicht beim Nageltest.
Langlebiger, weniger temperaturempfindlich
Von der Sicherheit abgesehen hat LFP noch weitere Vorteile: So verspricht BYD auch nach 3.000 Zyklen noch eine Kapazität von 90 Prozent und darüber und die Temperaturempfindlichkeit ist erheblich geringer als bei Li-NMC. BYD sagt, die Blade Batterie funktioniere zwischen -35 und +55 Grad Celsius prima. Den Hauptvorteil dürften aber die Kosten bilden: Eisenphosphat ist günstig zu bekommen, während der E-Auto-Boom neben Lithium vor allem Nickel und Mangan stark verteuert hat.
Noch günstiger herzustellen sind Natrium-Batterien, die entsprechend nicht mal mehr Lithium brauchen. Das geht an BYD nicht vorbei: Die BYD-Tochter Findreams hat mit der Huaihai Holding Group ein Joint Venture gegründet, um eine Produktion für Natrium-Ionen-Batterien in Xuzhou in der Provinz Jiangsu zu errichten. Medienberichten zufolge haben die beiden Unternehmen am 8. Juni 2023 in Shenzhen eine entsprechende strategische Kooperationsvereinbarung unterzeichnet.
Know-How der Zellproduktion von NMC übertragbar
Die Leistung von BYD ist die Entwicklung des Aufbaus der Blade-Batterie, die die Chinesen in nächster Stufe bereits im Cell-to-body-Verfahren nutzen, also direkt in die Karosserie des Fahrzeugs einbauen, wie es BMW beispielsweise für die Neue Klasse angekündigt hat. Die kommt aber mit besonders großen Rundzellen von CATL erst 2025 und setzt weiterhin auf NMC – gut für die Energiedichte, schlecht für die Kosten.
Bei der Produktion hingegen konnten die Chinesen auf ihr Know-how mit Li-NMC zurückgreifen, denn die Herstellung wirkt grundsätzlich nicht großartig anders. Das lässt sich bei einem Besuch in BYDs Giga-Factory beobachten. Die Stationen der Batterieproduktion sind, wie gehabt, das Mixen des sogenannten Slurry (Pampe) für Anode und Kathode, das sogenannte Coating, also Bestreichen der Folien, die anschließend mehrfach gepresst und getrocknet werden.
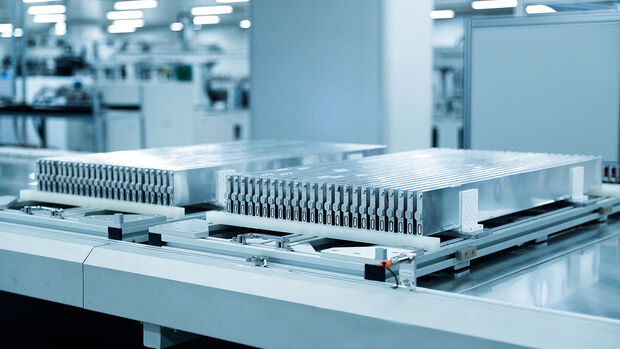
Je nach Modell fasst BYD eine dreistellige Zahl von Blades zu einem Akku zusammen.
Dabei überwachen die Experten unter Zuhilfenahme empfindlicher Sensoren und Messgeräte ständig die Ergebnisse. Zu guter Letzt schneiden Maschinen die Folien zu. In mehreren Schritten werden sie verschweißt, aber das Blade-Gehäuse bleibt bis zum Schluss offen, denn es muss noch unter hohem Druck der Elektrolyt injiziert werden und dessen Lösungsmittel muss durch weiteres Trocknen verdunsten. Die Trockenöfen brauchen bei der Batterieproduktion am meisten Strom. Bei BYD kommt er aus dem lokalen Netz, der CO₂-Eintrag bei der Produktion der Blade-Batterien ist also grundsätzlich auch nicht geringer – die Stromerzeugung aus regenerativen Quellen bleibt die zentrale Aufgabe für jede Art von Batterieherstellung.
Gigafactory – Vorsprung vor europäischen Autoherstellern
Die BYD-Giga-Factory steht in Chongqing, gut zwei Flugstunden nordwestlich von Shenzen. Etwas außerhalb der Kernstadt hat BYD am 24. Februar 2019 mit dem Bau seiner Giga-Factory begonnen. Das dauerte angeblich nur ein Jahr. Das Unternehmen hat dafür nach eigenen Angaben drei Milliarden Euro investiert. Die Bauzeit erstaunt vor allem, wenn man sich die Dimensionen der Anlage vor Augen führt: Auf einer Fläche von gut 22 Quadratkilometern arbeiten und leben hier 17.000 Mitarbeiter, davon 7.000 Ingenieure – die Unterkünfte hat BYD gleich mitgebaut.
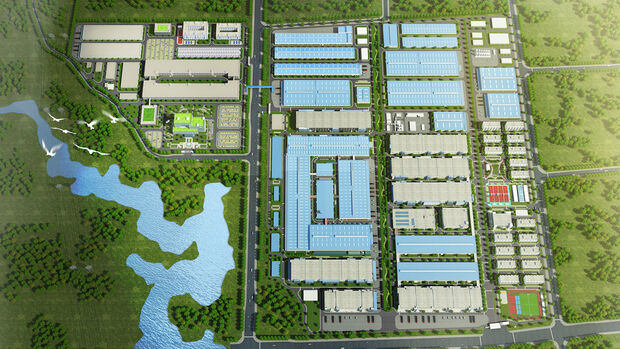
Die Blade-Batterie-Fabrik steht auf einem Gelände von gut 6 Quadratkilometern.
Dank seiner Findreams-Entwickler hält BYD laut eigenen Angaben allein 8.000 Patente im Batterie-Bereich und hat 5.000 davon vergeben. Die Fabrik stößt jährlich Batterien mit einer Kapazität von 22 GWh aus und täglich im Zwei- bis Dreischichtbetrieb 90.000 Zellen – an sechs Tagen der Woche. Bezogen auf den BYD Han wären das 500 Akkupacks pro Tag.
Fazit
BYD begann vor 28 Jahren in der Elektronikproduktion und kam so zur Akkuherstellung. Mit der Blade-Batterie haben die Chinesen für eine günstige Zellchemie einen Akku-Aufbau nicht nur so entwickelt, dass eine automobiltaugliche Energiedichte möglich ist, sondern Sie produzieren die neuen Batterien günstig und vor allem massenhaft. Das ist im E-Auto-Markt der entscheidende Punkt – von Wunderbatterien aus Laboren hört man oft, deren Produktion im großen Maßstab liegt hingegen oft in ungewisser Zukunft.
Weil 40 Prozent der Wertschöpfung von E-Autos auf den Akku zurückgeht, konnte sich BYD auf dem schnell wachsenden E-Automarkt in China eine marktbeherrschende Stellung erarbeiten: Jedes dritte E-Auto oder PHEV-Fahrzeug kam dort im ersten Halbjahr 2023 von BYD. Und mit dem Joint Venture zur Herstellung von Natrium-Akkus könnte der Vorsprung noch wachsen.