Wir hatten in der Simulation am Anfang der Entwicklung Zweifel, ob das Auto so sicher werden würde, wie ich es immer vorhatte. Deshalb ist die Dachspinne mit A-, B- und C-Säule, die wir auf die Alu-Karosserie schrauben, aus hochfestem Stahl – aus Crashsicherheits-Gründen. Das ist auch der Grund, warum unser Chassis nicht ganz so günstig geworden ist, wie wir erwartet hatten. Heute weiß ich, dass es übertrieben war, denn die späteren Crashergebnisse waren einfach klasse. Die Aktion hat mir auch die Zielkosten für mein im Ursprung sensationell günstiges Auto etwas verhagelt.
Die meisten setzen auf die Automatisierung des Montageprozesses. Das sieht schön und robotisiert aus, rechnet sich aber quasi nie – jedenfalls nicht in Stückzahlen unter 100 000 Fahrzeugen pro Jahr. Wir kalkulieren mit bis zu 70.000 Einheiten eines Typs pro Jahr. Unsere Fabrik ist in der Montage quasi komplett manuell – nicht nur in der Vorserienproduktion. Aber der Informations- und Datenfluss ist zu 95 Prozent automatisiert – von der frühen Spezifikation an. Ich kann aus diesem Auto in weniger als zwölf Monaten ein Cabrio sowie unterschiedliche Radstandversionen machen – als reine Derivate-Entwicklung. Das Besondere ist, dass wir über all diese Systeme hinweg eine eigene Datenbasis als Extrakt haben – den digitalen Schatten. Das ist unser Kernelement der Industrie-4.0-Infrastruktur.
Heute können Sie normalerweise nicht einfach so auf den Konfigurator zugreifen. Kundenkonfiguration und Produktkonfiguration laufen nicht in einem System. Eine Bestellung erfolgt also über einen kompletten Systemwechsel. Allein die Fehlbestellungen durch Übertragungsfehler sind ein echter Wertverlust. Bei uns können Sie das Auto auf dem Handy konfigurieren und zu einer echten Bestellung machen. Die geht dann direkt in die Produktion. In einem klassischen Montagewerk wird bei jeder Umstellung (Change Request) viel Zeit durch Suchen oder Warten verloren – diese Zeitverluste möchte ich heben. Bei uns ist also der Informationsfluss automatisiert, nicht der Montageprozess. Und die Batterie muss günstig sein, das heißt klein und einfach. Nach den Passagieren ist die Batterie auch das sensibelste Teil.
Die muss wasserdicht abgeriegelt sein, umhüllt mit einem Panzer, nur so schafft man die maximale Sicherheit, und wir haben keine Batterieheizung oder -kühlung. Einen Kühler haben wir nur für den Motor. Wir machen dem Kunden nach acht Jahren ein attraktives Angebot für den Austausch der Batterie, weil wir die alte Batterie an Solaranlagenbetreiber weiterverkaufen können. Die mögen Autobatterien, weil die besonders robust sind. Und ich bekomme noch gutes Geld dafür.
Dann noch mal bis zu 20 Jahre. Eigentlich geht eine Lithium-Ionen-Batterie gar nicht kaputt, wir verlieren nur über die Zeit Zellen, und dann verschlechtert sich das Leistungsgewicht. Es sind bei uns noch Rundzellenbatterien, für die unser Lieferant 2.500 Vollladezyklen garantiert. Wenn Sie also pro Jahr 14.000 Kilometer fahren, was mit so einem Auto schon eher viel wäre, dann kommen Sie über acht Jahre auf diese 2.500 Vollladezyklen.
Doch, bei einem Elektroauto brauchen Sie kaum Vorderwagen. Aber dann fangen die Leute an, sich unwohl zu fühlen, das haben wir schon beim StreetScooter-Projekt gelernt. Deshalb haben wir bewusst mehr Vorbau eingeplant, als notwendig gewesen wäre. Wir haben übrigens 44 Zentimeter Knautschzone. Das ist in etwa so viel wie bei der Mercedes S-Klasse. Das Ergebnis eines der schwierigsten Crashszenarien mit 40 Prozent Überdeckung sieht wirklich sensationell aus.
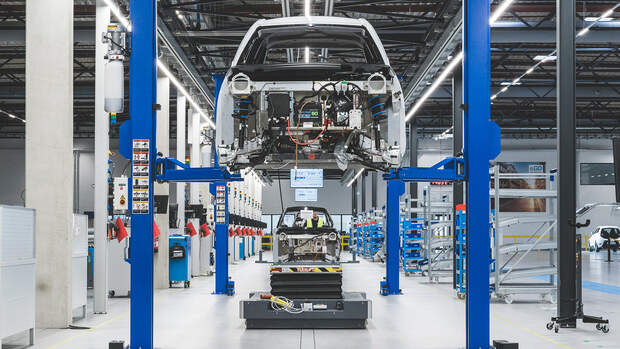
Weil die Heckpassagiere sehr weit hinten sitzen. Die fangen wir damit sehr gut ab. Das ist aktuell im Kleinwagenbau so ziemlich das Solideste, was Sie sich vorstellen können. Und das war unsere Absicht. Dieses Auto lebt sehr, sehr lange. Aber es kommt halt mit diesen Produkten, die auch nach vielen Jahren noch ihren spezifischen Wert haben, in einen ökologischen Kreislauf. Warum schmeißen wir heute nach zehn Jahren und 200.000 Kilometern ein Auto weg? Weil sich aufgrund des Verschleißes ein neues Aggregat nicht lohnt. Aber dann wird gleich das komplette Auto entsorgt.
Sie brauchen gegenüber Lack die vierfache Kraft, um sie überhaupt zu beschädigen. Und wenn sie beschädigt wird, sieht man es oft gar nicht so richtig, weil ja keine Grundierung freigelegt wird. Und anstatt um die 30 Millionen Euro Entwicklungs- und Werkzeugkosten nur für die Leuchten vorne und hinten auszugeben, wie das oft bei Premium-Herstellern der Fall ist, haben wir Leuchten aus dem Standardregal genommen. Die kosten zum Beispiel hinten um die 25 Euro das Stück.
Vom Fahrverhalten ist der E.Go wie ein Porsche 911. Wir haben eine sensationelle Erfindung reaktiviert, das ist die De-Dion-Hinterachse, wie sie im Opel Diplomat verbaut war. Das ist die robusteste Starrachse, die sich im Fahrverhalten anfühlt wie eine Einzelradaufhängung. Das Auto fährt sich wie auf Schienen. 70 Prozent der aktuellen elektrisch betriebenen Kleinwagen haben Frontantrieb. Das ist falsch. Ein Elektroauto kann gar nicht mehr gut werden, wenn es Frontantrieb hat. Dann ist der ganze Spaßfaktor weg, weil man Traktionsprobleme bekommt.
Weil beide bei schnellen Kurvenfahrten das kurveninnere Vorderrad anheben, das heißt eine negative Wankachse haben. Wir schaffen eine unglaublich hohe Querbeschleunigung. Das macht das Auto zum perfekten Gokart. Eine teure Verbundlenker-Hinterachse könnte das nicht besser.
Ja. Ich habe langsam Angst, dass ich keine Vorbestellungen mehr annehmen kann. Wir haben 3.200 Vorbestellungen, mehr geht nicht, weil wir alle Vorbesteller noch in 2019 beliefern wollen.
Wir werden noch weitere Modelle auflegen. Wir haben gerade die E.Go REX GmbH als Brennstoffzellen-Range-Extender-Hersteller gegründet, um serielle Plug-in-Hybridantriebe für den Elektro-Kleinbus E.Go Mover mit einem kleinen, kompakten 22- bis 30-kW-Brennstoffzellen-Aggregat ausrüsten zu können. Wir haben mit einem Aachener Konsortium noch ein fünfsitziges geräuschloses Flugzeug in der Konzeption, das auch autonom fliegen kann. Und dann denken wir noch über einen elektrischen Lkw nach.
Ich kann mir für die Zukunft nicht vorstellen, dass wir mit 40-Tonnern unterwegs sind, die dann nur 32 Tonnen Zuladung haben, weil da sechs oder acht Tonnen Batterie drinstecken. Das kann nicht sein. Dafür ist die Ökobilanz der Batterie zu schlecht. Und kommen wir zur Infrastruktur: Auch wenn die Firma Tesla sagt, sie könne ihre Trucks in 50 Minuten laden – das geht ja nur mit drei oder vier Megawatt. Wo soll das passieren? Und wer bezahlt die Infrastruktur? Das erscheint mir nicht logisch. Und seien wir ehrlich: Große Dieselmotoren, auch wenn sie sauber sind, werden in Städten in Zukunft kritisch gesehen. Deswegen glaube ich, dass auch hier der Hybridantrieb die eigentliche Lösung ist. Hier kommt auch die Brennstoffzelle als Range Extender zum Zuge.
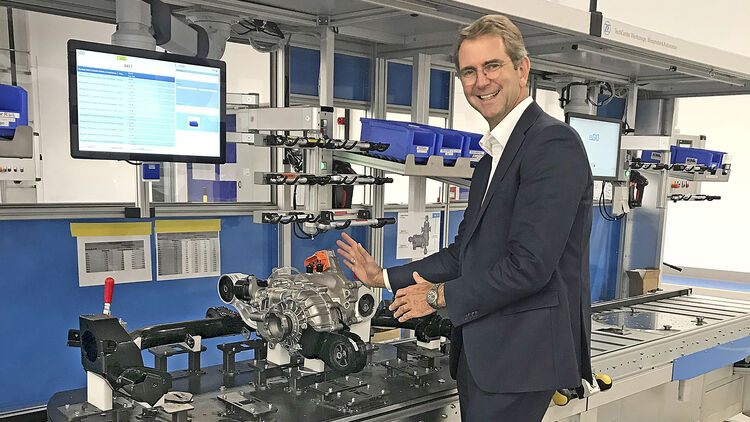
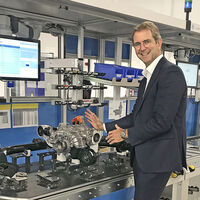
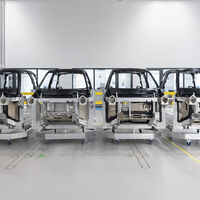
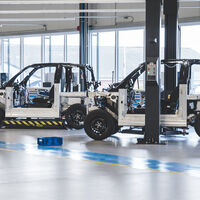
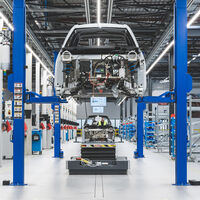
Bei den Kosten. Der größte Teil der Brennstoffzelle ist heute nicht industriell skaliert. Der Fundamentalfehler ist, das Brennstoffzellen-Auto zum Gegenentwurf des E-Autos zu machen. Der Motor zieht seinen Strom aus der Brennstoffzelle, er muss also lastvariabel ausgelegt werden. Eine Brennstoffzelle mag aber keine Lastwechsel – egal wie ich ihr das anerziehe. Ich brauche also eine Krücke und viel mehr Kühlung. Die Kosten der Stacks skalieren fast linear mit der Leistung. Wir haben da auch lange diskutiert. Wir haben uns jetzt entschlossen, ein konsequent als Range Extender ausgelegtes Brennstoffzellen-System in aller Konsequenz zu industrialisieren und zu skalieren und dann auch Dritten für ihre Fahrzeuge anzubieten. Wir brauchen Stückzahlen. Ich hätte die Brennstoffzelle auch gerne bei den bekannten Herstellern eingekauft. Aber da gab es nichts.
Es ist erstaunlich, zu beobachten, dass viele Hersteller in der Endphase ihrer Entwicklungsprojekte entweder rechts oder links falsch abbiegen. Die Brennstoffzelle war vor Kurzem noch nahezu verpönt. Und anstatt sich über den Mercedes GLC F-Cell zu freuen, rümpft die Branche die Nase und sagt: Damit kann man ja gar kein Geld verdienen.