Wir haben durch BMW i sehr früh mit BEVs angefangen. Aber auch der Markt für PHEVs ist mindestens so wichtig, deswegen setzten wir auf beide Konzepte.
Die PHEVs der ersten Generation hatten Reichweiten, bei denen sich das Laden nur für wenige Einsatzprofile lohnte. Ganz anders beispielsweise beim neuen X5 mit Plug-in-Hybrid-Antrieb. Damit kommt man auch im Realbetrieb mit einer Ladung rein elektrisch 60 bis 70 Kilometer weit, entsprechend hoch ist der elektrische Fahranteil. Der X5 PHEV ist sehr beliebt bei unseren Kunden. Ich bin sicher, spätestens mit den künftigen Reichweiten von etwa 100 Kilometer im Zyklus wird der elektrische Fahranteil auf 50 bis 60 Prozent steigen. Alle sind sich einig, dass der PHEV wichtig ist, um jetzt großflächig zu elektrifizieren: Sie machen sich auf Langstrecken unabhängig von Ladeinfrastruktur. Denjenigen, die Vorbehalte haben, was Reichweite und die Ladeverhältnisse angeht, ermöglicht der PHEV immer öfter elektrisch zu fahren. Er hat außerdem volks- und betriebswirtschaftlich eine Relevanz, weil der Übergang von der einen in die andere Technologie nicht über Nacht passieren wird. Auch, wer im Sinne der Beschäftigungssicherung argumentiert, wird daher Sympathien für diese Technologie haben.
Mit Blick auf den E-Antrieb ist es uns wichtig, dass wir gemeinsam mit den Lieferanten die Zell-Chemie der Zukunft definieren. Das entspricht im Übrigen unseren Entwicklungsprinzipien, das machen wir mit einem Getriebelieferanten ganz genauso: Wir verstehen jeden Schaltmechanismus, den ZF in seine Automatik einbaut, unsere Applikateure wissen genauestens, was in diesem Getriebe passiert und optimieren es gemeinsam mit dem Lieferanten. Das macht uns auch wertvoll als Partner in der Industrie. Und das sehen wir bei den Batteriezellen ganz genauso.
Aus heutiger Sicht werden wir keine Batteriezellen für unsere Serienfahrzeuge selbst produzieren, insbesondere nicht, weil die Technologie hier im Fluss ist. Es wäre nicht der richtige Moment, jetzt indie Produktion einzusteigen.
Den Prozess zu verstehen, was die beste Zelle ausmacht, ist essenziell. Unser Batteriezell-Kompetenzzentrum evaluiert die gesamte Wertschöpfungskette: Wie skaliert die Fertigung hoch, welche kommerziellen Effekte und welche Qualitätsauswirkungen hat sie? Wir werden das sogar noch erweitern, weil am Ende nicht nur die beste Chemie darüber entscheidet, was die beste Zelle ist, sondern ihre Industrialisierung für die Produktion ist mindestens genauso wichtig. Meldungen über neue Kathoden- oder Anoden-Materialien die eine doppelte Reichweite ermöglichen kommen inzwischen fast im Wochentakt von den Hochschulen. Das funktioniert auch – im Labor. Für uns ist aber die Frage: Wie können sie Millionen dieser besten Zelle automatisiert in perfekter Qualität von einer Fertigungsstraße laufen lassen? Deswegen werden wir künftig auch hier in München seriennah Prototypenzellen produzieren, um genau den Prozess in der Lieferantenstruktur abzubilden, so dass wir auch bei der Industrialisierung mit den Lieferanten komplett auf Augenhöhe sprechen können. Die Batteriemodule bauen wir ohnehin inhouse.
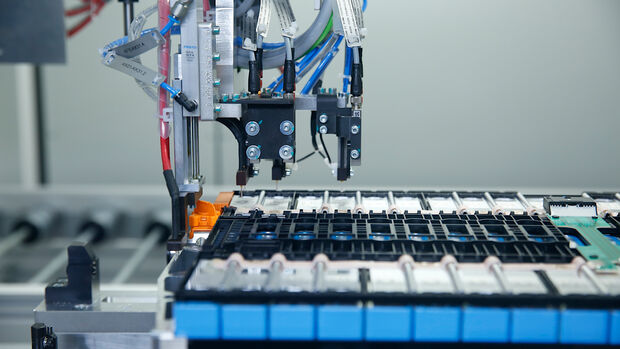
Ganz klar: Die entwickeln wir selbst und bauen sie selbst in Dingolfing. Wir entwickeln übrigens auch die Leistungselektronik inhouse.
das so sein. Beim iX ist das anders. Wie gehen sie denn künftig mit dem Wandel zur E-Mobilität bei ihren Fahrzeugarchitekturen um?
Der iX steht noch nicht auf einer neuen Architektur, sondern auf einer eigenen, reinen E-Plattform. Aber seine Komponenten, E-Antrieb, Motoren, Hochvoltspeicher werden beispielsweise auch beim nächsten 7er und 5er auf der flexiblen CLAR-Architektur mit allen vier Antriebsarten Verwendung finden. Ab der zweiten Hälfte des Jahrzehnts erwarten wir eine deutlich steigende Elektrifizierung, deshalb fangen wir turnusgemäß jetzt an, die Nachfolge-Architektur zu entwickeln. Diese neue Architektur wird den Fokus vom Verbrenner auf elektrische Antriebe verschieben. Wir wollen uns auch mit dieser zukünftigen Architektur eine Flexibilität bei den Antriebsvarianten erhalten – für Details ist es jetzt noch zu früh. Trotzdem ist das ein ziemlich großer Sprung und nicht nur ein rein entwicklungstechnisches Thema, sondern eine 360-Grad-Aufgabe aus kommerziellen, industriellen und ästhetischen Herausforderungen. Dafür haben wir eine neue Abteilung gegründet, die diese Vernetzung im Unternehmen sicherstellt und erstmal an unseren Vorstandsvorsitzenden Oliver Zipse direkt berichtet.
Nein, das ist genau der richtige Zeitpunkt. Sie kommt ab der zweiten Hälfte der 20er-Jahre und ist genau der richtige Weg, wie wir dann den Markt bedienen wollen. Auch für die erste Hälfte sind wir gut unterwegs. Wir sind in Europa und weltweit die Nummer 1 bei Plug-in-Hybriden (PHEVs). Für BMW ist es essenziell, erster im Mainstream zu sein. Es ist eines der wichtigsten Entwicklungsprinzipien von BMW, schon um eine Ecke geschaut zu haben, während sich die anderen noch draufzubewegen. Das ist uns auch schon häufig gelungen. Wir waren immer ganz vorne dabei, wenn es zum Beispiel um den Einsatz von Sensorik, Ethernet und Software-Upgrades geht – das ist nun alles Maistream.
Die wird vergleichbar mit der Produktlinien-Organisation. Sie steuert alle damit verbundenen Bereiche. Was zur Festlegung der neuen Architektur organisatorisch passiert, ist eine Produktlinie der frühen Phase, die neue Architektur löst ja dann auch irgendwann die alte ab. Die Mitarbeiter bleiben daher im Prinzip, wo sie sind, wie bei der Digital-Entwicklung auch.
Als BMW i 2006 entstanden ist, war ja auch der Auftrag völlig anders. Damals war der Zweifel, ob Elektro überhaupt jemals kommt, so groß, dass man mit dem Project i einen viel größeren Impuls setzen musste. Die Organisation war noch nicht so weit, dass sie diesen Schritt hätte mitgehen können. Jetzt brauchen wir keinen Impuls mehr. Wir überführen in eine neue Architektur, die dann auch den Kern von BMW bildet.
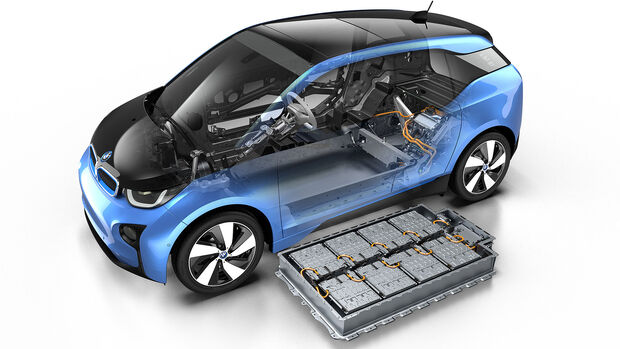
Wir machen dann etwas anders, wenn es funktional gut und sinnvoll ist. Der iX verkörpert das, wofür ein BMW steht. Wir haben hier jeden Vorteil, den die elektrische Architektur bietet, realisiert. Im Fond ist so viel Platz wie im X7, obwohl das Auto etwa so lang ist wie der X5. Der Boden ist flach, die Füße haben großzügig Bewegungsfreiheit. Das erweitere Platzangebot konnten wir erreichen, indem wir den Vorderwagen etwas kürzer gestaltet haben. Schließlich sitzt unter der Motorhaube lediglich die E-Maschine für die Vorderachse, die Ladelektronik und Sensorik anstelle eines platzintensiven Verbrennerantriebs.
Durch den Anstieg der E-Mobilität würden die CO2-Emissionen je Fahrzeug in der Lieferkette bis 2030 um mehr als ein Drittel steigen. Das möchten wir vermeiden und die CO2-Emission verglichen mit 2019 sogar um 20 Prozent senken. Dabei erzeugen wir Zellen und Module schon jetzt ausschließlich mit Grünstrom. Das heißt, E-Mobilität funktioniert nur, wenn wir die Wertstoffkreisläufe schließen. Sonst verlagern wir den CO2-Ausstoß lediglich – vom Fahren in die Produktion. Wir arbeiten bei der Produktion der Batterien mit Northvolt zusammen, beim Recycling ist es Umicore. Mit diesen Partnern bauen wir gerade einen europäischen Footprint auf, der den Kreislauf bis zum Recycling schließt.
Der Schlüssel zu ökologischem BEV-Fahren liegt in der Zelle, wie Sie diese herstellen und nach der Nutzung zur Wiederverwendung recyceln. Der Übergang in die BEV-Welt ist immer mit einem Wandel des gesamten Energiesystems verbunden. Die sogenannte Reichweitenangst können sie bis zu einer sinnvollen Schwelle natürlich mit mehr Reichweite lösen. Unserer Ansicht nach liegt diese Schwelle bei 500 bis 600 Kilometer. Der iX hat einen gut 100 kWh großen Speicher und erreicht durch seine hohe Effizienz diese Reichweite. Noch größere Speicher machen E-Autos nach heutigem Stand ökologisch fragwürdig.
Denken Sie an die engen Häuserschluchten in Tokyo oder Seoul: Hier kann eine für Wasserstoff umgebaute Tankstelle hunderte Fahrzeuge versorgen. Dasselbe ausschließlich mit E-Ladeinfrastruktur zu erreichen, wäre deutlich aufwändiger. Zumal ein Großteil der Stromversorgung durch oberirdische Leitungen läuft. In Deutschland haben wir unterirdische Leitungen und ein sehr stabiles Stromnetz – aber selbst hier wird uns der Ausbau Jahrzehnte beschäftigen. In bestimmten Regionen und Marktsegmenten ist Wasserstoff in der Tat wenig sinnvoll. In anderen dagegen sehr – zum Beispiel in unseren oberen Segmenten wie dem X5. Mein Lieblingsbeispiel ist Japan: Dort hat die Politik früh auf Wasserstoff gesetzt, übrigens wie Korea. Es gibt bereits eine gute Tankinfrastruktur. Und die Voraussetzungen in den Metropolen sind anders als bei uns.
Ganz im Gegenteil: Damit wird jeder BMW digitaler denn je. Die Digitalisierung ist eine große Herausforderung für eine klassische, maschinenbauliche Industrie wie die unsere. Bislang war alle Intelligenz, das Gehirn der Funktionen im Auto. Mit dem Shift hin zu datengetriebenen Entwicklungen und Backend-Funktionen wandert das Gehirn quasi aus dem Auto heraus in die Cloud. Das verändert die ganze Industrie. Wir haben das Digitale natürlich nicht erst mit dem iX für uns entdeckt, sondern schon mit dem 7er vor 20 Jahren, der den meisten vor allem wegen seiner besonderen Heckdeckelgestaltung in Erinnerung geblieben sein dürfte. Der E65 war der erste Digitalisierungs-Enabler. iDrive, Menüführung, Steuergeräte, die es vorher gar nicht gab – das war für die damalige Entwicklung ein Meilenstein. Vermutlich würde BMW ohne dieses Auto heute nicht da stehen, wo wir jetzt stehen. Denn seine Entwicklung hat dazu geführt, dass wir der Digitalisierung schon vor Jahren viel Bedeutung haben zukommen lassen.
Wir haben inzwischen 14 Millionen Autos im Feld, vom 1er bis zum 7er, die vernetzt sind. In 2018 haben wir mit unserem Operating System 7 auch das Remote Software Upgrade eingeführt. Damit können wir unsere Flotte digital over-the-air updaten. Der Campus in Unterschleißheim, wo wir automatisiertes Fahren entwickeln, hat dann noch mal ganz andere Entwicklungslogiken eingebracht wie Künstliche Intelligenz oder agiles Arbeiten, die für die Umsetzung der Digitalisierung wichtig sind. Und als ich meine neue Position angetreten bin, haben wir uns gefragt: Wie wollen wir uns denn gesamthaft digital aufstellen? Bei der Konkurrenz gibt es derzeit eine Neigung zur Separierung, alle Softwareentwickler zusammengesetzt in einem Haus – aber das bedeutet, dass man die Digitalisierung aus den wesentlichen Funktionen herauszieht – und das ist genau das Gegenteil dessen, wie wir Autos entwickeln.
Nein. Wir haben gesagt, wir brauchen eine starke Stelle, die all diese Funktionen im Digitalbereich vernetzt. Seit 1.10.2020 gibt es deshalb die neue Organisation "Digital Car" als integrierter Teil des Entwicklungs-Ressorts. Wir haben etwa 10.000 dezidierte "Softwerker" verteilt in den verschiedensten Funktionen – Produktentwicklung, produktionsnahe Entwicklung, IT usw. Die Einheit Digital Car besteht aus drei großen Säulen: Hardware und Software, die wir bewusst nicht trennen, Connectivity also Oberflächen, Userinterface, Backend, und autonomes Fahren. Aber diese Prozesskette greift nicht nur auf ihre eigenen Leute zu, sondern hat eine unternehmensweite Aufgabe.
Der iX hat unseren neuen Technologiebaukasten an Bord, um die nächste Generation Fahrassistenzsysteme in den Markt einführen zu können. Wenn wir in der Kombination aus Sicherheit, Funktion und Verantwortungsübernahme durch das System einen echten Mehrwert für unsere Kunden sehen, werden wir die Option anbieten. Zudem ist der Gesetzgeber ein entscheidender Einflussfaktor, der erst klären muss wie er diese Technologie testet und bewertet. Wir müssen beim hochautomatisierten Fahren nachweisen, dass der Computer sicherer fährt als der Mensch. Das ist für uns die Referenzgröße. Der Nachweis ist mindestens um Faktor 1 Million komplexer als der in der Entwicklung bisheriger Fahrerassistenzsysteme.
Wir bieten in den USA bereits ein Assistenzsystem der Stufe 2 an, bei dem der Fahrer auf der Autobahn über längere Abschnitte die Hände vom Lenkrad nehmen kann – aber er muss weiter auf den Verkehr achten und das überwacht das Assistenzsystem mit einer Kamera im Cockpit. Das ist in USA rechtlich möglich und unsere Fahrzeuge beweisen täglich, dass das sicher funktioniert. Dennoch bleibt die Verantwortung beim Fahrer, anders als bei Stufe 3, wo man die Verantwortung an das Fahrzeug abgibt.
Zur Person
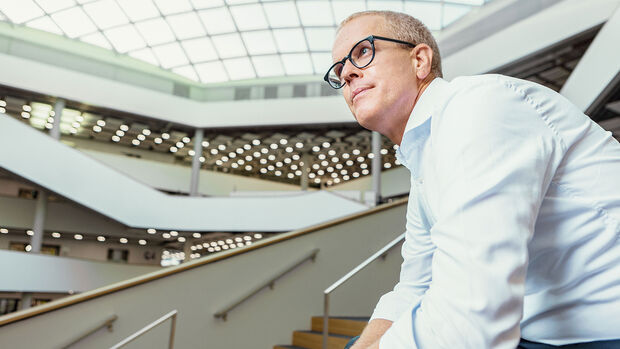
Frank Weber, Jahrgang 1966, Ist Maschinenbau-Ingenieur. Seine Karriere in der Automobilindustrie begann er 1991 bei Opel, wo er Direktor fürs Programm-Management und bis 2007 für Voraus- und Konzeptentwicklung war. Dann ging der Familienvater als Baureihenleiter für den Chevrolet Volt bzw. ersten Opel Ampera zur damaligen Opel-Mutter General Motors nach Michigan, USA (bis 2010). Nach einem weiteren Jahr bei Opel (Vice President Unternehmens- und Produktplanung) wechselte er als Leiter Entwicklung Gesamtfahrzeug zu BMW, war zuletzt Leiter Produktlinie Luxusklasse und Rolls-Royce. Seit 1. Juli 2020 ist der überzeugte Vegetarier Mitglied des Vorstands.